واضح آرشیو وب فارسی:تبیان: مواد (فلزات آهنی)
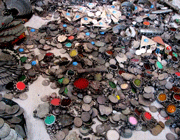
فلزات عناصر شیمیایی مانند آهن، طلا یا آلومینیوم هستند که با حل شدن در محلول اسیدی خالص حامل بار مثبت میشوند و در هسته الکتریکی به سوی قطب منفی حرکت میکنند. بیشتر فلزات رساناهای خوبی برای گرما و الکتریسیته و عموماً سخت، سنگین و مقاوم هستند. فلزات آهنیدر ساختمان فلزات آهنی عنصر آهن وجود دارد. ماشینکاران دیر زمانی است که با خاصیت های مفید آهن سروکار دارند. آهن: آهن خالص ( فریت ) عنصری نسبتاً نرم با ساختمان بلورین است. آهن خالص در 1527 درجه سانتیگراد به حالت جامد درمیآید و دما در طی زمان کوتاهی که بستگی به نرخ انجماد و جرم فلز دارد در این حد ثابت میماند. سپس دما به 898 درجه کاهش مییابد و در این حالت نیز وقفه دیگری در کاهش دما پیش میآید. با سرد شدن بیشتر تا 769 درجه باز هم دما برای زمان کوتاهی ثابت میماند. با کاستن دما از 769 درجه سانتی گراد تا دمای محیط توقف دیگری در افت دما پیش نمیآید.با سرد شدن آهن خالص تغییرات معینی در آن روی میدهد. آهن خالص چهار فاز جامد با خصوصیات فیزیکی متفاوت دارد. فازهای آهن خالص عبارتند از:1- آهن آلفا:این آهن نرم و مغناطیسی است و حلال کربن نیست. آهن آلفا در حد فاصل میان دمای محیط و 769 درجه سانتی گراد پدید میآید.2- آهن بتا:این فاز آهن در دماهای بالا دارای خاصیت مغناطیسی ضعیفی است ولی در دماهای پایین خاصیت مغناطیسی ندارد. به شدت سخت و شکننده است و تقریباً اثری بر کربن ندارد. آهن بتا بین 769 تا 898 درجه سانتیگراد به وجود میآید.3- آهن گاما:در این فاز آهن آماده حل کردن کربن است و حلالیت آن با افزایش دما بیشتر میشود. اگر سرد شدن آهن گاما همراه با عبور سریع از نقطه بحرانی باشد گذار آن از آهن گامای سخت به آهن آلفای نرم به تعویق میافتد. بنابراین در این حالت آهن از نظر سختی ناپایدار و آماده تبدیل به فاز نرم آلفاست.به نظر میرسد وجود مواد خارجی مانند کربن، نیکل و منگنز مقاومت آهن گاما را نسبت به تبدیل شدن به آهن آلفا افزایش میدهد و به این ترتیب آهن گاما در دماهای پایین مقاومتر و پایدارتر خواهد بود.از طرف دیگر وجود کرم، تنگستن، آلومینیوم، سیلیکون، فسفر، آرسنیک و گوگرد، گذار آهن سخت بتا به آهن نرم آلفا را ساده میکند. از نظر سختی آهن گاما در میان آهن آلفا و آهن بتا قرار دارد. آهن گاما در حد فاصل دماهای 898 و 1401 درجه سانتیگراد تشکیل میشود.4- آهن دلتا:این گونه آهن کاربرد بسیار کمی دارد. آزاد شدن حرارت در 1401 درجه سانتیگراد نشانه تغییر ساختمان داخلی فلز در گذار از فاز دلتا به فاز گاماست. نقطه بحرانی در 1401 درجه آشکار میشود و بنابراین در بالا و پایین نقطه بحرانی فازهای مختلف آهن تشکیل میشوند. آهن دلتا در حد فاصل دماهای 1401 و 1528 درجه سانتیگراد به وجود میآید. آهن خام:ترکیبی از آهن، کربن و سیلیکون، گوگرد، فسفر و منگنز است. مقدار کربن موجود در آهن خام 2 تا 5/4 درصد است که به دو صورت شکل میگیرد، بخشی به صورت محلول یا ترکیبی و بخش دیگر در سراسر جرم فلز به شکل گرافیت یا کربن غیرترکیبی پخش میشود.
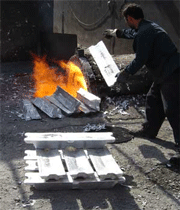
چدن:چدن با فشار شکل نمیگیرد و با نورد و کشش به شکلهای مفید درنمیآید. این آهن در واقع آهن خام است که دوباره ذوب شده است. مقدار کربن موجود در چدن بیش از 2 درصدی است که به این ترتیب فلز چدن در هیچ دمایی چکشخوار نیست. چدن در صنایع ریختهگری کاربرد فراوان دارد و دارای چهار نوع است:1- چدن خاکستری: این نوع چدن در ریختهگری معمولی بیشترین کاربرد را دارد. این چدنِ نرم دارای درصد بالایی از گرافیت است که موجب سفتی و از سوی دیگر مقاومت کششی اندک آن میشود. چدن خاکستری در هنگام شکست با دانهبندی درشت به رنگ تیره یا خاکستری میگسلد. این رنگ ناشی از ورقههای پهن گرافیت است که در سراسر ماده پخش شدهاند. اگر ورقههای گرافیت بزرگ و فراوان باشند مقاومت کششی چدن اندک است. اندازه و مقدار ورقههای گرافیت از چگونگی شکلگیری آنها در هنگام انجماد تأثیر میپذیرد. اگر سرعت انجماد زیاد باشد کربن کمتری به شکل گرافیت جدا میشود. بنابراین سختی ماده بر اثر افزایش میزان کربن ترکیبی زیاد میشود. چدن خاکستری دارای 5/2 تا 5/3 درصد کربن است. 2- چدن سفید:آهن با درصد کربن کم (2 تا 5/2 درصد) آهن سفید نامیده میشود. این آهن در تمام طول ریختهگری کربن ترکیبی خود را کاملاً حفظ میکند و بنابراین گرافیت تشکیل نمیشود. در نتیجه آهن حاصل از ریختهگری بسیار سخت و شکننده خواهد بود. از آهن سفید هنگامی برای ساخت قطعات ماشین استفاده میشود که مطلوب، سختی باشد و شکنندگی مسألهای ایجاد نکند.اگر گرافیت هم کموبیش تشکیل شود لختههای تیرهای در آهن سفید مشاهده خواهد شد و در این مناطق سختی کاهش مییابد. این آهن، چدن خالدار نامیده میشود.3- چدن چکشخوار:برای ساخت قطعات پیچیده دستگاه ها و در مواردی که نرمش ماده ضرورت داشته باشد از چدن چکشخوار بیش از گونههای دیگر استفاده میشود. قطعات ریختگی ساخته شده از چدن چکشخوار را میتوان در محدوده تحمل این ماده بدون ایجاد شکستگی خم کرد.قطعات ریختگی از چدن سفید سخت و شکننده ساخته میشوند و پس از فرایند تافتن تبدیل به چدن چکشخوار میشوند. در فرایند تافتن کربن اضافی بر اثر عملیات حرارتی طولانی در دمای 899 درجه سانتی گراد حذف میشود. با گذشت چند ساعت کربن گرافیتی جذب و چدن به گونهای فولاد تبدیل میشود. 4- آهن چکشخوار:بنابر تعریف این ماده نوعی فولاد کم کربن است که مقدار زیادی سرباره دارد. آهن چکشخوار از نظر روش ساخت با فولاد فرق دارد و فرق آن در این است که هنگام تولید کاملاً ذوب نمیشود. این آهن دارای 1 تا 2 درصد سرباره است. برای تولید آهن چکشخوار از آهن سفید استفاده میشود و ناخالصی ها در فرایند همزنی حذف میشوند.با وجود گوگرد آهن چکشخوار شکننده و بر اثر حرارت سرخشکن میشود. فسفر در دمای معمولی موجب سردشکنندگی آهن میشود. آهن چکشخوار در 870 درجه سانتی گراد نرم و قابل جوشکاری است و در دماهای پایینتر نیز همچنان امکان چکشکاری آن وجود دارد. فولاد:تعبیری کلی و بیانگر آلیاژهایی است که فلز پایه آن ها آهن و مهم ترین عنصر افزودنی آن ها کربن است. فولادهای ساده آلیاژهایی از آهن و کربن هستند که از صفر تا 2 درصد کربن دارند و عنصر دیگری در ساختمان آن ها شرکت نمیکند. از نظر کمیّ، فولاد خالص ( آلیاژ آهن و کربن ) هیچ گاه ساخته نمیشود.در فولادهای کربنی ساده تجارتی سومین عنصر آلیاژی منگنز است. مقادیر کمی سیلیکون، فسفر، گوگرد و مقدار ناچیزی از سایر عناصر نیز در این فولاد یافت میشود. فولادهای کربنی ساده دارای چند صدم تا 4/1 درصد کربن هستند و خاصیت های آن ها بستگی به میزان کربن و عملیات حرارتی دارد.
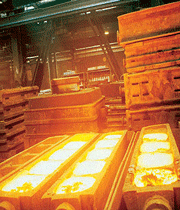
بیشتر فولادهای کمکربن به شکل نورد شده و یا پس از تافتن به کار میروند. ولی از فولادهای پرکربن در مواردی استفاده میشود که سختی زیاد لازم باشد. افزایش میزان کربن فولاد تا درصد معینی مقاومت آن را بالا میبرد ولی پس از این حد از مقاومت فولاد کاسته میشود. برای مثال فولاد 1/0 درصد کربن دارد و مقاومت کششی آن در حدود 35 کیلوگرم بر میلیمترمربع است. وجود 2/1 درصد کربن استحکام را تا 98 کیلوگرم بر میلیمترمربع میافزاید که مقاومت خوبی برای فولادهای کربنی است. با وجود 2 درصد کربن مقاومت کششی به حدود 63 کیلوگرم بر میلیمترمربع میرسد و با افزودن تدریجی میزان کربن، ماده با سرعت خصوصیات چدن را کسب میکند.فولادهای کربنی ساده بندرت بیش از 4/1 درصد کربن دارند. حد بالای کربن موجود در این فولادها از دیدگاه نظری 2 درصد است. افزون بر کربن عناصر دیگری برای کسب خصوصیات بهتر به فولاد اضافه میشوند. نتیجه افزودن این عناصر به شرح زیر است:1- فسفر سختی فولاد را برمیافزاید و در برابر ساییدگی مقاومتر میکند. فولاد با درصد فسفر بالا در برار ضربه و تنشهای ارتعاشی ضعیف است. بنابراین فسفر برای ورق های دیگ بخار ناخالصی زیانباری به شمار میرود. 2- گوگرد بر شکلدهی و چکشخواری فولاد اثر میگذارد زیرا شکنندگی فولاد را در دماهای بالا افزایش میدهد و فولاد ((سرخشکن)) میشود. میزان گوگرد موجود در فولاد نباید بیش از 02/0 تا 05/0 درصد باشد.3- منگنز مقاومت، سختی و یکنواختی فولاد را برمیافزاید. اگر نسبت منگنز در فولاد بالا باشد فولاد سختی و شکنندگی ویژهای کسب میکند که در این حالت برش آن بسیار دشوار است. یک اثر دیگر منگنز بر فولاد خنثیسازی است.4- نیکل موجب افزایش مقاومت و سفتی فولاد میشود.5- آلومینیوم یکنواختی شمش ها و قطعات ریختگی را بهتر میکند.6- وانادیم مقاومت فولاد را در برابر خستگی برمیافزاید. با وجود وانادیم نرمش فولاد بسیار بالا میرود و مقاومت کششی و حد کشسانایی آن نیز افزایش مییابد و پایداری فولاد در برابر ضربه بسیار زیاد میشود.میزان وانادیم موجود در فولادها از 16/0تا 25/0 درصد است. این فولاد در فنرها، محور ماشینها، چرخدندههای سنگین بار و تمام قطعاتی که باید در برابر ارتعاش ثابت و تنش های متغیر مقاوم باشند فراوان به کار میرود.فولادهای وانادیمداری که کرم نیز در ترکیب آن ها وجود داشته باشد در بسیاری از قطعات خودرو، فنرها، محورها، میللنگ ها و چرخدندهها به کار میروند. بیشتر فولادهای دارای کرم- وانادیم 2/0 تا 6/0 درصد کربن نیز دارند. بسیاری از قطعات محصول آهنگری گرم که روی آن ها عملیات حرارتی انجام میشود از این فولادها ساخته میشوند.7- با وجود مولیبدن در ترکیب فولاد، فولادهای تندبُر به دست میآیند. فولاد مولیبدندار برای ساخت میللنگ های بزرگ، میلگاردان، تفنگ های بزرگ، لوله تفنگ و صفحات دیگ های بخار مناسب است. دلیل نام گذاری فولاد تندبُر آن است که با استفاده از این فولاد در ابزارهای برنده مانند ابزارهای ماشینتراش، برش فلز با سرعت بیشتری انجام میگیرد. تندبُر در دماهای بالا سختی خود را از دست نمیدهد. ابزارهایی که از جنس این فولاد باشند در سرعت هایی که لبههای ابزار داغ میشود به خوبی کار میکنند.فولادهای تندبُر دارای 12 تا 20 درصد تنگستن، 2 تا 3 درصد کرم، معمولاً 1 تا 2 درصد وانادیم و گاه حاوی کبالت نیز هستند. میزان کربن این فولادها بسیار کم ( عموماً 65/0 تا 75/0 درصد ) است. فولاد 1-4-18 بیشتر از سایر گونههای موجود کاربرد دارد. این فولاد 18 درصد تنگستن، 4 درصد کرم و یک درصد وانادیم دارد. گونه مناسب دیگر این فولاد 2-4-14 است. فولادهایی که 18 درصد تنگستن دارند معمولاً بهترین نوع فولاد به شمار میروند. از طرف دیگر فولادهایی که تنگستن کمتری دارند ارزانتر هستند.
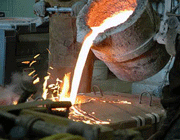
اگر عملیات حرارتی و کارهای تکمیلی مناسبی روی فولاد ضد زنگ انجام شود این فولاد به خوبی در برابر اکسیده شدن و خوردگی پایداری می کند. فولاد ضدزنگ کاملاً نسبت به خوردگی مقاوم نیست. ابزارهای دندانپزشکی و جراحی و کاردهای ضدزنگ دارای 12 تا 14 درصد کرم هستند.در صنایع ریختهگری فولاد ریختگی از چدن قویتر است. فولادهای ریختگی ساخته شده از فولاد ضدزنگ در دماهای حدود 982 درجه سانتیگراد و بیش از آن ( بسته به میزان کرم موجود در ترکیبشان ) نسبت به اکسیداسیون مقاومت میکنند.فولاد ریختگی با همان سرعت چدن درقالب ریخته نمیشود. کاهش حجمی ( انقباض ) فولاد ریختگی در هنگام سرد شدن بیش از چدن است زیرا ریختهگری این نوع فولاد در دماهای بالا انجام میشود. به همین دلیل در طراحی قطعات ماشین باید از ایجاد تغییرات ناگهانی در جدارهها خودداری کرد. دانش نامه ماشین کاری 1 - ریس میلرگروه مدرسه اینترنتی سایت تبیان- تنظیم : سمیرا بادامستانی
این صفحه را در گوگل محبوب کنید
[ارسال شده از: تبیان]
[مشاهده در: www.tebyan.net]
[تعداد بازديد از اين مطلب: 429]