محبوبترینها
آیا میشود فیستول را عمل نکرد و به خودی خود خوب میشود؟
مزایای آستر مدول الیاف سرامیکی یا زد بلوک
سررسید تبلیغاتی 1404 چگونه میتواند برندینگ کسبوکارتان را تقویت کند؟
چگونه با ثبت آگهی رایگان در سایت های نیازمندیها، کسب و کارتان را به دیگران معرفی کنید؟
بهترین لوله برای لوله کشی آب ساختمان
دانلود آهنگ های برتر ایرانی و خارجی 2024
ماندگاری بیشتر محصولات باغ شما با این روش ساده!
بارشهای سیلآسا در راه است! آیا خانه شما آماده است؟
بارشهای سیلآسا در راه است! آیا خانه شما آماده است؟
قیمت انواع دستگاه تصفیه آب خانگی در ایران
نمایش جنگ دینامیت شو در تهران [از بیوگرافی میلاد صالح پور تا خرید بلیط]
صفحه اول
آرشیو مطالب
ورود/عضویت
هواشناسی
قیمت طلا سکه و ارز
قیمت خودرو
مطالب در سایت شما
تبادل لینک
ارتباط با ما
مطالب سایت سرگرمی سبک زندگی سینما و تلویزیون فرهنگ و هنر پزشکی و سلامت اجتماع و خانواده تصویری دین و اندیشه ورزش اقتصادی سیاسی حوادث علم و فناوری سایتهای دانلود گوناگون
مطالب سایت سرگرمی سبک زندگی سینما و تلویزیون فرهنگ و هنر پزشکی و سلامت اجتماع و خانواده تصویری دین و اندیشه ورزش اقتصادی سیاسی حوادث علم و فناوری سایتهای دانلود گوناگون
آمار وبسایت
تعداد کل بازدیدها :
1856559312


بازیابی فاضلاب نیروگاه های بخاری
واضح آرشیو وب فارسی:راسخون:
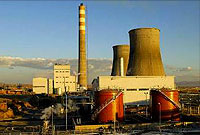
بازیابی فاضلاب نیروگاه های بخاری یکی از آلودگیهای مهم در کلیه فعالیتهای صنعتی و از جمله نیروگاههای برق،فاضلابهای صنعتی است که ضروری است بطور اصولی کنترل شوند تا علاوه بر جلوگیری از اثرات سوء آن، در مصرف منابع محدود آبی کشور نیز صرفهجویی شود. بطور کلی در صنایع و نیروگاههای برق (که در این مقاله نیروگاههای بخاری مورد نظر است) با فرآیندهای تکمیلی، میتوان براحتی بخش عمدهای از فاضلاب تولید شده در نیروگاهها را به منظور استفاده مجدد در فرآیندهایی که نیاز به آب دارند، برگردانده و به مصرف رسانید. ضرورت استفاده از آب جبرانی در سیکل آب و بخار و سیکل خنککننده نیروگاههای بخاری و بخصوص در نیروگاههایی که از برجهای خنککنتر استفاده میکنند این واحد صنعتی را جزء پرمصرفترین صنایع از نظر مدیریت منابع آبی قرار داده است. بر طبق آمارهای موجود میزان مصرف آب مورد نیاز برای یک نیروگاه بخاری با برج خنککنتر در هر مگاوات معادل ۲ تا ۳ متر مکعببر ساعت تخمین زده شده است که این روند مصرف آب و تولید فاضلاب با توجه به رشد سریع تولید برق در کشور به شدت رو به افزایش است. از این رو با بازیابی فاضلاب نیروگاه میتوان تا حدی بالا بودن مصرف آب کل نیروگاه را جبران کرد. فاضلابهای نیروگاهی فاضلابهای صنعتی در یک نیروگاه بخاری عمدتاً از نظر کیفی به چهار دسته فاضلابهای نمکی شامل انواع نمکهای محلول، فاضلابهای سمی (در موارد شستشوهای شیمیایی تجهیزات)شامل فلزات سنگین، بازدارندهها و دترجنتها، فاضلابهای لجنی شامل ذرات معلق ناشی از تخلیه زلالسازها و شستشوی معکوس فیلترها و فاضلابهای آلوده به سوخت و روغن تقسیم میشود. فاضلابهای نمکی اغلب محتوی ترکیبات سولفاتها، سولفیتها، نیتراتها، کلرورها، فسفاتها، کربناتها، بیکربناتها و ... هستند. این فاضلابها از نظر شکل ظاهری شفاف بوده و بدون هیچگونه رنگ و طعم هستند ولی به دلیل بالا بودن مقدار املاح محلول در آن قابل استفاده مجدد نبوده و یا جهت تخلیه به محیطزیست مناسب نیستند. فاضلابهای لجنی شامل کلیه مواد معلق و رسوبات موجود در درین زلالسازهای بخش تصفیه مقدماتی آب و شستشوی معکوس فیلترهای فیزیکی هستند. این فاضلابها از نظر شکل ظاهری شفاف نبوده و تیره هستند و در مواردی به شکل لجن آب در فرآیندهای مختلف تولید میشوند که برخلاف گونه اول از املاح محلول کمتری برخوردار بوده ولی به دلیل وجود ذرات معلق بالا در آن، قابل استفاده مجدد یا جهت تخلیه به محیطزیست مناسب نیستند. فاضلابهای سمی شامل فلزات سنگین از قبیل وانادیم، نیکل، کرم، کبالت، کادمیم، آهن، مس و ترکیبات آلی بازدارنده و دترجنتهای مورد مصرف در شستشوهای شیمیایی تجهیزات مختلف نیروگاه هستند. این فاضلابها هم تیره بوده و هم از املاح محلول بالایی برخوردار هستند که به دلیل وجود مواد سمی، تخلیه آنها به محیط زیست مجاز نیست. فاضلاب آلوده به سوخت تنها در نیروگاههای با سوخت مایع تولید میشود که قسمت عمدهای از آن ناشی از نشت تجهیزات از قبیل دستگاههای منتقلکننده سوخت،پمپها و لولههای انتقال، نشت گرمکنهای سوخت و غیره است. بخش دیگر تولید فاضلاب آلوده به سوخت به شستشوی محوطه تخلیه سوخت تانکرها و مخازن مربوطه برمیگردد. اما اغلب، مهمترین عامل تولید این فاضلاب، دریناژ منابع سوخت است که بسته به میزان آب وارد شده به منابع،در ماه یک تا چند بار تخلیه میشود. آب ورودی به این تانکها در اکثر موارد مربوط به نشتی کویلهای بخار در منابع است و معمولاًجهت جداسازی از به هدر رفتن مقادیر قابل توجه سوخت، از تله سوخت استفاده میشود. تله سوخت با استفاده از اختلاف دانسیته سوخت و آب، سوخت را از آب جدا کرده و مجدداً به منابع باز میگرداند. حجم این فاضلابها کم بوده و جزء دسته فاضلابهای آلوده به روغن بشمار میروند. فاضلاب آلوده به روغن معمولاًاز تجهیزاتی که به نوعی با روغن (یا به عنوان عامل خنککننده و یا عامل روانکننده) سروکار دارند نشت کرده و از طریق شستشو و یا عوامل دیگر با آب مخلوط شده و جاری میشود. حجم این گونه فاضلابها در نیروگاهها بالا نبوده و بعضاً در مواردی با استفاده از سیستم جداساز ثقلی آب و روغن تصفیه میشوند. بصورت کلی و خلاصه عناوین فاضلابهای صنعتی در یک نیروگاه بخار عبارتند از: ▪ فاضلاب درین زلالسازها ▪ فاضلاب شستشوی معکوس فیلترهای فیزیکی ▪ فاضلاب احیا مبدلهای یونی (در تصفیهخانه آب خام و تصفیه خانه میان راهی سیکل آب و بخار) ▪ فاضلاب پس زد مدولهای اسمز معکوس ▪ فاضلاب بلودان تبخیرکنندهها ▪ فاضلاب برجهای خنککننده تر ▪ فاضلاب آلوده به سوخت و روغن ▪ فاضلاب شستشوی محوطه سالنها و کارگاهها آمادهسازی و تصفیه فاضلاب با توجه به گستردگی ترکیبات فاضلابهای نیروگاهی نسبت به فاضلابهای بهداشت،روشهای تصفیه آن نیز به همان میزان گسترده است. در تصفیه فاضلابهای بهداشتی یا شهری معمولاً مواد آلی، COD BOD و مواد معلق و کلوئیدی از مهمترین پارامترهای طراحی و بهرهبرداری محسوب میشوند، در حالی که با وجود پارامترها و ترکیباتی چون فلزات سنگین، روغن و گریس و موادشناور، ترکیبات محلول و تنوع مشخصهها در فاضلابهای نیروگاهی که تعیینکننده بوده و انتخاب و طراحی سیستم را از حالت کلیشهای خارج میکند، لازم است برای هر مورد خاص طرح مناسب برای همان مورد در نظر گرفته شود و طراحیها صورت پذیرند. تصفیه فاضلابهای لجنی به روش تهنشینی در این نوع تصفیه که از نوع تهنشینی مجزا یا منفرد است قوانین سقوط ذرات از معادله استوکس تبعیت میکند. این حوضچهها معمولاًبه اشکالی با سطوح مقاطع مستطیلی و دایرهای ساخته میشوند. اصول و مبنای طراحی در این حوضچهها به نوع ذرات معلق محتوی فاضلاب و میزان راندمان تهنشینی وابسته است به عبارت دیگر با مشخص کردن بار سطحی ذرات و زمان ماند فاضلاب در این حوضچهها که تابع عوامل نوع ذره و میزان راندمان تهنشینی ذرات است سطح و عمق حوضچه محاسبه و مشخص میشود. در این بخش، ذرات قابل تهنشین در این حوضچهها جدا شده و ذرات غیرقابل تهنشینی به همراه فاضلابهای سمی و کدر به روش انعقاد و لختهسازی تصفیه میشوند. تصفیه فاضلابهای آلوده به سوخت و روغن معمولاً برای حذف سوخت و روغن از فاضلابهای آلوده به این مواد در نیروگاهها و دیگر صنایع از حوضچههای چربیگیر یا حوضچههای شناورسازی استفاده میکنند. این جداکنندهها دارای انواع مختلفی در صنعت است. سادهترین و پرمصرفترین نوع آن استفاده از جداکنندههای API (انستیتو نفت آمریکا) است. جهت بالا بردن راندمان حذف ذرات روغن از جداکنندههای با صفحات مورب استفاده میکنند. این سیستمها به دلیل استفاده از صفحات مورب در منطقه جداسازی و ایجاد سطح تماس بیشتر از راندمان بهتری برخوردار هستند. نوع دیگر این سیستمها استفاده از جداکنندههای با تزریق هوای فشرده هستند که به دلیل ایجاد کمک به صعود ذرات روغن به سمت بالا راندمان عمل جداسازی افزایش مییابد. آب تصفیه شده از این سیستم (جداسازی روغن و سوخت) به منظور انجام مراحل بعدی تصفیه به همراه فاضلابهای سمی و کدر به سیستم انعقاد ولختهسازی هدایت میشود. تصفیه فاضلابهای سمی و کدر به روش انعقاد و لختهسازی استفاده از روشهای فیزیکی و شیمیایی (انعقاد و لختهسازی)از دیرباز در مباحث تصفیه فاضلابهای صنعتی و آب خام مطرح بوده است. وجود ذرات معلق و ترکیبات فلزات سنگین در این دسته از فاضلابها ضرورت استفاده از روشهای انعقاد و لختهسازی و ترسیب شیمیایی را مشخص میکنند. این فرآیند متشکل از چندین واحد است که به ترتیب عبارتند از: واحد تنظیم PH، واحد اختلاط سریع،واحد لختهسازی، واحد تهنشینی، واحد تغلیظ لجن،واحد آبگیری از لجن،واحد فیلتراسیون و واحد خنثیسازی. در صورتی که فاضلاب ورودی به این فرآیند از نظر کیفی و کمی دارای تغییرات زیادی باشد استفاده از یک واحد متعادلساز جریان فاضلاب قبل از ورود به فرآیند مورد نیاز است. آب تصفیه شده در این سیستم کاملاً شفاف بوده و مشکل اصلی آن نمکهای محلول در آن است. دیاگرام جمعآوری فاضلابهای نیروگاه به منظور بازیابی فاضلاب خروجی از واحد انعقاد و لختهسازی،فاضلاب احیای مبدلهای یونی، واحد اسمز معکوس و تبخیرکنندهها در تصفیهخانه آب خام نیروگاه جزء فاضلاب نمکی بوده و مشکل اصلی آنها وجود املاح بالا در آنها است این فاضلاب تقریباً شفاف بوده و از کدورت پایینی برخوردار است. یکی از روشهای متداول، جهت حذف آلایندههای محلول در فاضلاب، تبخیر فاضلاب و تقطیر آن است. تبخیر فاضلاب در نیروگاهها که معمولاً حجم آن نیز کم نیست از طریق تبخیر طبیعی و تبخیر دستگاهی قابل انجام است. آب تصفیه شده از فاضلاب آلوده به سوخت و روغن به همراه آب سریز واحد تهنشینی و فاضلاب سمی و کدر نیروگاه به واحد انعقاد و لختهسازی و ترسیب شیمیایی وارد میشود این واحد همانطوری که در مباحث قبلی ذکر شده، از چندین واحد تشکیل شده است. آب زلال خروجی از این واحد به همراه فاضلاب نمکی نیروگاه به واحد تبخیر دستگاهی هدایت میشود. در این واحد پس از تغلیظ در دستگاه تبخیرکننده پساب به استخرهای تبخیر طبیعی هدایت میشود. لجن جمعآوری شده در این سیستم به همراه لجن بخش تهنشینی و لجن خروجی از واحد انعقاد و لختهسازی به مراکز دفن هدایت میشوند. آب مقطر خروجی از این سیستم نیز جهت استفاده مجدد و تامین آب جبرانی سیکل آب و بخار به تصفیهخانه آب مرکزی هدایت میشود. سیستمهای تبخیرکننده جهت تغلیظ پساب نمکی با توجه به کمبود منابع آبی و نیاز نیروگاهها به آب مقطر،میتوان با استفاده از سیستمهای تبخیری،بخارات حاصل از سیستمهای مذکور را تقطیر کرده و آب مقطر حاصل را به مصرف نیروگاه رسانید. از طرف دیگر با وجود هزینه بسیار بالای تولید آب بییون از آب خام و تفاوت اندک بین هزینه سرمایهگذاری سیستمهای تبخیری و روش تبخیر طبیعی، تولید آب مقطر از این طریق مقرون به صرفه خواهد بود. سیستم مذکور شامل فرآیندهای تبخیر و تقطیر است که مشابه سیستمهای شیرینسازی آب دریا است. اساس فرآیندهای تقطیر در سه مرحله کاملاًجدا به شرح زیر است: ۱) ایجاد بخار با افزودن انرژی حرارتی به پساب ۲) خارج کردن بخارات حاصله از محیط عملیاتی ۳) تقطیر کردن بخارات مذکور عملیات تبخیر و تقطیر را در سیستمهای مختلفی میتوان انجام داد،که ذیلاًبه برخی از آنها اشاره میشود و در نهایت سیستم منتخب معرفی میشود. سیستم تبخیری ساده در سیستم مذکور، دو فرآیند اصلی تبخیر و تقطیر،در دو محفظه جداگانه به اجرا در میآیند. آب ناخالص و یا پساب مورد نظر در محفظه اول، تبخیر شده و بخارات حاصل در محفظه دوم تقطیر میشوند. در داخل هر محفظه،یک سری لوله وجود دارد که در سیستم تبخیری،آب گرم و در سیستم تقطیری،آب سرد در آنها جریان دارد. در دو انتهای هر سری از لولهها، بخش جمعآوری آب قرار دارد که ارتباط بین آب ورودی و خروجی از لولهها را برقرار میسازد. آب در داخل لولههای تبخیرکننده با گرفتن حرارت بخاری که در داخل پوسته در جریان است، تبخیر شده و بخارات موجود در پوسته، مایع میشوند، بخارات تولیدی وارد کندانسور شده ودر آنجا در اثر تماس با سطوح سرد لولههای کندانسور،مایع میشوند و به عنوان محصول از سیستم خارج میشوند. جهت تامین آب لولههای کندانسور و صرفهجویی در ورود آب اضافی به سیستم،از پساب نمکی جهت سرد کردن بخارات کندانسور استفاده میشود، آب خروجی نسبتاًگرم بوده و پس از خروج از کندانسور، به دو بخش تقسیم میشود، بخشی وارد لولههای تبخیرکننده شده و بخشی دیگر تخلیه میشوند. آب ورودی به لولههای کندانسور و دستگاه تبخیرکننده، باید شرایطی جهت عملکرد بهینه سیستم داشته باشد،از جمله اینکه، میزان آن در حدی باشد که بتواند حرارت انتقالی از بخارات موجود در لولههای تبخیرکننده به جریان ورودی به کندانسور را جذب کند. در مورد سیستم تبخیرکننده نیز آب ورودی باید برابر مقدار بخار تولید شده بعلاوه مقدار خروجی از تبخیرکننده باشد. در ضمن مقدار پساب تغلیظ شده از دستگاه باید بگونهای باشد که غلظت املاح و ناخالصیهای موجود در آن از حد اشباع بیشتر نشده تا از ایجاد رسوب در سیستم جلوگیری شود. سیستم تبخیر چند مرحلهای در برخی موارد به منظور افزایش بازده و بهرهوری دستگاه تبخیر ساده، میتوان با سری قراردادن چند تبخیرکننده مقدار مشخصی از بخار اولیه را چند برابر کرد که در این صورت به منظور حصول اطمینان از انتقال حرارت، فشار در بخشهایی که بخار تولید میشود متوالیاً در مقادیر کمتر نگاه داشته خواهد شد، بدین لحاظ،فشار داخل لولههای آخرین تبخیرکننده، کمترین و در اولین تبخیرکننده بیشترین مقدار خواهد بود. تبخیرکننده اول، همانند یک تبخیرکننده ساده و یکمرحلهای عمل میکند، انرژی حرارتی مورد نیاز را از بخاری که دستگاه مولد بخار تولید میکند، گرفته و آب داخل لولهها است. از این رو با توجه به این که بخار تولیدی در داخل لولهها درجه حرارتی برابر با درجه حرارت آب را دارند، بنابراین درجه حرارت و فشار بخار تولیدی در دومین تبخیر کننده پایینتر از بخار تولیدی در اولین تبخیرکننده است، به همین ترتیب، بخار تولیدی در تبخیرکننده دوم، وارد پوسته تبخیرکننده سوم شده و نهایتاً بخار خروجی از آخرین تبخیرکننده در کندانسور مایع میشود. سیستم تبخیر ناگهانی چند مرحلهای یکی دیگر از روشهای اقتصادی که در سیستمهای تقطیر وجود دارد، روش تبخیر ناگهانی است، بدین معنی که با کاهش ناگهانی فشار مایعی که قبلاً حرارت دیده و درجه حرارتش به نقطه جوش رسیده است،تبخیر صورت میگیرد. آب تغذیه ورودی تحت فشار، تا حدی که بخار نشود حرارت دیده و سپس در ماکزیمم درجه حرارت مورد نظر، با کاهش فشار در چندین مرحله،مقداری بخار در هر مرحله تولید میشود. با کندانس کردن تمام این بخارات،محصول مورد نظر حاصل میشود. پساب مورد نظر، وارد لولههای مرحله نهایی شده و توسط بخار موجود در مخزن تبخیر ناگهانی که در زیر لولههای کندانسور قرار دارد،گرم میشود. آب خروجی از این مرحله،به دو بخش تقسیم میشود. بخشی بعنوان خنککننده تخلیه می شود و بخشی دیگر پس از مخلوط شدن با پساب خروجی از پمپ به گردش درآورنده،وارد مرحله بعدی میشود،پس از طی مراحل بعدی،آب وارد مبدل حرارتی میشودکه در آن جا تا حد ماکزیمم گرم میشود،حرارت مورد نیاز مبدل نیز مانند مبدلهای سیستمهای قبل، از طریق منبع بخار خارجی تامین میشود. فشار پساب داغ با عبور از اریفیس کاهش یافته و به صورت اشباع واردمخزن تبخیر ناگهانی میشود. با کاهش فشار، پساب سرد شده و همزمان مقداری بخار تولید شده و وارد پوسته کندانسور میشود و با انتقال حرارت میان پوسته و لولهها،تقطیر صورت میگیرد میعانات در قسمت زیرین پوسته کندانسور جمع شده و از طریق یک اریفیس وارد پوسته کندانسور بعدی میشوند. بخشی از پساب داعی که بخار نشده است نیز وارد مخزن تبخیر ناگهانی مرحله بعدی میشود که مجدداً فرآیند تولید و تقطیر بخار تکرار میشود، میعانات تشکیل شده و پساب داغ در مراحل بعدی که به صورت سری هستند جداگانه جریان داشته و با گذشت هر یک از مراحل،مقدار جریان میعانات بیشتر شده و جریان پساب کاهش مییابد. خروجی مرحله آخر دو جریان است: ۱) میعانات که همان محصول سیستم هستند ۲) بخشی از پساب که از طریق پمپ خارج میشود. سیستم تبخیر و تقطیر بخار فشرده در سیستم مذکور با استفاده از کمپرسور،گرمای نهان تبخیر از قسمت تبخیر سطوح انتقال حرارت به قسمت کندانسه آن سطوح منتقل میشود و عملکرد آن برخلاف سیستمهای قبل، که اساس آن تنزل تدریجی انرژی گرمایی از درجه حرارت بالا به درجه حرارت پایین است، طرحریزی شده است. در فرآیند مورد نظر، بخار تولیدی از آب، تا حدی فشرده میشود که از کندانس شدن آن،حرارت مورد نیاز جهت تولید بخار اضافی از همان آب بدست آید. فرآیند اصلی شامل بخار شدن، جدا کردن بخارات از مایع و تقطیر بخارات حاصله، بوضوح مشخص است. یک مبدل حرارتی نیز،به منظور گرم کردن ورودی از طریق سردکردن پساب خروجی و محصول وجود دارد. انتخاب روش بهینه با مقایسه و بررسی اجمالی سیستمهای شرح داده شده، نکات زیر استخراج میشوند: ۱) سیستم تبخیر یک مرحلهای: در شرایطی کارآمد است که ظرفیت پساب مورد نظر کم باشد همچنین بخار فراوان و ارزان در دسترس باشد و از نظر تامین آب خنککن مشکلی وجود نداشته باشد. این روش بخصوص در مواردی بکار میرود که از بخار استفاده دیگری نتوان کرد. ۲) سیستم تبخیر چند مرحلهای: با بکارگیری این سیستم در انرژی گرمایی صرفهجویی میشود،از این رو هزینه سرمایهگذاری در این سیستم بالاتر است،البته میزان آب خنک مصرفی در حدود سه برابر محصول است. ۳) سیستم تبخیر ناگهانی چند مرحلهای: میزان آب خنککن این سیستم در حدود ۷ تا ۸ برابر محصول بوده واگر دسترسی به آب خنککن کافی میسر نباشد، باید با سرمایهگذاری گزافی از برجهای خنککن خشک استفاده شود که سبب محدودیت در کاربری سیستم میشود. ۴) سیستم تبخیر و تقطیری بخار فشرده: در این سیستم نیازی به آب خنک و بخار منبع خارجی نیست و از آنجا که پارامترهای طراحی این سیستم مانع از تغلیظ کافی پساب نمیشوند،این سیستم هم از نظر استفاده از آب خنککن و هم از جهت تغلیظ تا حداکثر درصد مورد نظر، بهینه است. در این روش حداکثر تا ده برابر میتوان پساب را تغلیظ کرد و باقیمانده پساب را که ۱۰ درصد حجم اولیه را دارد، در حوضچههای تبخیری جهت تکمیل فرآیند تبخیر وارد میکند. در ادامه با توجه به مزایای سیستم تبخیر و تقطیر بخار فشرده و نحوه عملکرد آن، سیستم تبخیرکننده با استفاده از تراکم مجدد بخار معرفی میشود. این فرآیند توسط نرمافزار Hysys شبیهسازی شده و قابل پیادهسازی است. فرایند مذکور ۴ مرحله اصلی شامل: ۱) حرارت دادن پساب ۲) دو فاز شدن ۳) جداسازی فاز مایع و بخار ۴) کمپرس کردن بخار تولید شده، را دنبال میکند. به منظور جلوگیری از مصرف انرژی اضافی در سیستم و در نتیجه استفاده بهینه از انرژیهای موجود از اصول تکنولوژی پینچ میتوان بهره گرفت. تکنولوژی پینچ، روشهای اصولی جهت استفاده بهینه و یا استفاده مجدد از انرژیهای موجود بین پروسههای یک فرآیند صنعتی را پیشنهاد میکند که این روشها بر اساس قوانین اول و دوم ترمودینامیک هستند و از طریق آنها میتوان نقاط تقاطع رژیمهای جریان سرد و گرم یک سیستم (به عنوان نمونه مبدل حرارتی) را مشخص و مرتفع کرد. در یک مبدل حرارتی با هدف کاهش دمای گرم در صورتی که دمای جریان سرد از حد مورد نیاز پایینتر باشد و یا بالعکس جهت افزایش دمای جریان سرد، دمای جریان گرم ازحد مورد نیاز بالاتر باشد، به منظور حفظ راندمان و کاهش اختلاف دمایی دو جریان مذکور، میتوان بااستفاده از تکنولوژی پینچ،نقطه پینچ مبدل ( که در آن اختلاف درجه حرارت بین دو جریان حداقل است) را محاسبه کرد. در واقع در این حالت حداقل مقدار انرژی لازم و یا حداقل اختلاف پتانسیل بین دو جریان،جهت انتقال حرارت تامین میشود که با بازیابی حرارتی ماکزیمم در مبدل، میتوان به هدف اصلی و اولیه آنالیز پینچ دست یافت. بدین ترتیب میتوان ۴۰-۱۵ درصد در هزینههای مصرف انرژی یک فرایند و ۱۵-۵ درصد در هزینههای سرمایهگذاری اولیه، صرفهجویی کرد. با توجه به این مطالب و همچنین افزایش راندمان تولید محصول،موارد زیر در طراحی سیستم در نظر گرفته میشود. الف) در کل فرآیند از مبدلهای حرارتی به جای گرمکنها و خنککنها استفاده میشود که در این صورت از مصرف انرژی اضافی جلوگیری بعمل میآید. با توجه به اصول تکنولوژی پینچ،دو مبدل اول،در ابتدای فرآیند، به منظور گرم کردن خوراک پیش از ورود به مبدل اصلی، تعبیه شدهاند بگونهای که از انرژی گرمایی موجود در محصول و پساب تغلیظ شده، استفاده شده و در نتیجه از مصرف انرژی اضافی در گرمکنها و خنککنها صرفهجویی میشود. ب) بازگرداندن بخشی از جریان مایع خروجی از برج جداکننده و اختلاط آن با خوراک پیش از ورود به مبدل اصلی، سبب افزایش راندمان جداسازی در سیستم میشود. به منظور راهاندازی و شروع به کار فرآیند به یک جریان بخار راهاندازی نیاز است که با گذشت زمان و افزایش بخار تولیدی در فرآیند، مقدار آن کاهش یافته و به صفر میرسد. فرآیند مذکور در مقیاس پایلوت و با جریان خوراک ۴۵۰ لیتر در ساعت، طراحی و اجرا شده است که در ادامه تشریح میشود. پساب نمکی با دمای ۲۰ درجه سانتیگراد و فشار اتمسفر یک به میزان ۴۵۰ لیتر در ساعت وارد پوسته مبدل اول میشود. در لولههای این مبدل مایع خروجی از مبدل اصلی فرآیند که در واقع همان میعان بخار راهاندازی است، جریان دارد که پس از شروع به کار سیستم جریان موجود در لولهها، همان محصول نهایی سیستم خواهد شد که با دمای ۹۲ درجه سانتیگراد وارد لولهها شده و پس از انتقال حرارت به پساب موجود در پوسته، با دمای ۵۰ درجه سانتیگراد از مبدل خارج میشود. پساب پس از افزایش دما تا ۵۳ درجه سانتیگراد وارد پوسته مبدل دوم میشود و حرارت لازم را برای افزایش درجه حرارت از گرمای پساب غلیظ شده موجد در لولهها (با دمای ۱۰۰ درجه سانتیگراد)گرفته و در درجه حرارت حدود ۶۲ درجه سانتیگراد از مبدل خارج میشود. این امر همانطور که در قبل نیز اشاره شد مصداق دیگری از استفاده بهینه از انرژی است که با بازگشت جزیی از جریان خروجی از برج جداکننده (جریان پساب غلیظشده) از هدر رفتن حرارت وانرژی موجود دراین جریان جلوگیری بعمل میآید. پساب پس از اختلاط با جزء دیگر جریان خروجی از برج جداکننده که توسط پمپ سیرکولاسیون در گردش است وارد مبدل اصلی فرآیند میشود که پس ازجذب حرارت لازم و رسیدن به مرحله دو فازی با دمای حدود ۱۰۰ درجه سانتیگراد وارد برج جداکننده میشود که جریان خروجی از بالای برج در فاز بخار و جریان خروجی از پایین برج بصورت مایع (پساب غلیظ شده) است. به منظور افزایش انرژی حرارتی بخارات خروجی از برج جداکننده و در نتیجه افزایش بهرهوری مبدل اصلی از کمپرسوری استفاده میشود که جریانی با فشاری در حدود kp۲۱۶ و با دمای ۲۲۰ درجه سانتیگراد تامین میکند. جریان مذکور وارد لولههای مبدل اصلی شده که پس از انتقال حرارت و رسیدن به دمای ۹۱ درجه سانتیگراد از طریق یک شیر فشارشکن به فشار اتمسفریک رسیده و وارد مبدل اول میشود که این جریان پس از گذر از مبدل اول با دمای ۵۰ درجه سانتیگراد بعنوان محصول از سیستم خارج میشود. پساب تغلیظ شده نیز با دمای ۵۶ درجه سانتیگراد و در فشار اتمسفریک از مبدل دوم خارج شده و به سمت استخرهای تبخیری هدایت میشود. نتیجهگیری: با توجه به مطالب ذکر شده در مباحث پیشین و اهمیت برگشت و استفاده مجدداز فاضلاب نیروگاهها لزوم استفاده از فرایند بازیابی وتولید آب مقطر از فاضلاب نیروگاه مشخص میشود. همانطور که در این فرآیند مشاهده میشود حدود ۸۰ درصد از فاضلاب ورودی به این فرآیند به محصول آب مقطر تبدیل میشود و تنها ۲۰ درصد آن به عنوان فاضلاب تغلیظ شده از فرآیند خارج میشود که به دلیل عدم انطباق شاخصهای کیفی پساب تغلیظ شده با استانداردهای ملی سازمان حفاظت محیطزیست ایران به منظور تخلیه به محیطزیست لازم است که این پساب به استخرهای تبخیر طبیعی هدایت شود. حال اگر به عنوان نمونه یک نیروگاه MW۴×۲۵۰ با سیستم برج خنککنندهتر را در نظر بگیریم بطور تقریبی در حدود ۲۵۰۰ متر مکعب بر ساعت آب خام مصرف میشود که در حدود ۹۰۰ متر مکعب بر ساعت طی فرآیندهای مختلف به فاضلاب نمکی تبدیل میشود. باورود این حجم فاضلاب به فرآیند بازیابی، در حدود ۷۰۰ متر مکعب بر ساعت آب مقطر تولید میشود که مابقی آن به دلیل وجود املاح بسیار بالا به استخرهای تبخیر طبیعی تخلیه و رسوبات جمعآوری میشود. در کل مزایای بکارگیری فرآیند بازیابی فاضلاب نیروگاه با استفاده از تبخیرکننده با تراکم مجدد بخار را میتوان به شرح زیر اعلام کرد. ۱) جلوگیری از تخلیه فاضلابهای مختلف نیروگاه به محیطزیست ۲) تولید آب مقطر به منظور تامین بخشی از آب مصرفی نیروگاه ۳) کاهش حجم فاضلاب نمکی ورودی به استخر تبخیر طبیعی و در نتیجه صرفهجویی اقتصادی در احداث آن ۴) صرفهجویی در برداشت منابع آبی کشورمهندس امیرسهرابی کاشانیمهندس روشنک ریاضی منبع:https://www.aftab.ir/
این صفحه را در گوگل محبوب کنید
[ارسال شده از: راسخون]
[مشاهده در: www.rasekhoon.net]
[تعداد بازديد از اين مطلب: 780]
صفحات پیشنهادی
بازیابی فاضلاب نیروگاه های بخاری
بازیابی فاضلاب نیروگاه های بخاری یکی از آلودگیهای مهم در کلیه فعالیتهای صنعتی و از جمله نیروگاههای برق،فاضلابهای صنعتی است که ضروری است بطور اصولی ...
بازیابی فاضلاب نیروگاه های بخاری یکی از آلودگیهای مهم در کلیه فعالیتهای صنعتی و از جمله نیروگاههای برق،فاضلابهای صنعتی است که ضروری است بطور اصولی ...
آب با طعم غلیظ نفت!
22 نوامبر 2011 – بازیابی فاضلاب نیروگاه های بخاری بر طبق آمارهای موجود میزان مصرف آب مورد نیاز برای یک نیروگاه بخاری با برج ... این فاضلابها از نظر شکل ظاهری ...
22 نوامبر 2011 – بازیابی فاضلاب نیروگاه های بخاری بر طبق آمارهای موجود میزان مصرف آب مورد نیاز برای یک نیروگاه بخاری با برج ... این فاضلابها از نظر شکل ظاهری ...
ماهی ها قاتل می شوند!
بسیاری از افراد برای انجام این کار به تعمیرگاه های ویژه مراجعه می کنند اما برخی دیگر ... این رابطه مطرح است، تخلیه نادرست روغن موتور در چاه فاضلاب یا داخل جوی های آب است ... که این روغن های بازیابی شده را آن هم با قیمت گران تر از روغن موتور نو بخرند! ... به عنوان سوخت در توربین های کوره های نیروگاه های برق، کوره های کارخانه های سیمان و ...
بسیاری از افراد برای انجام این کار به تعمیرگاه های ویژه مراجعه می کنند اما برخی دیگر ... این رابطه مطرح است، تخلیه نادرست روغن موتور در چاه فاضلاب یا داخل جوی های آب است ... که این روغن های بازیابی شده را آن هم با قیمت گران تر از روغن موتور نو بخرند! ... به عنوان سوخت در توربین های کوره های نیروگاه های برق، کوره های کارخانه های سیمان و ...
زمینه های امنیت جهانی در عصر انتظار
زمینه های امنیت جهانی در عصر انتظار نويسنده: فهیمه رئوف چکیدهانتظار، امری پر اهمیت در عصر غیبت امام زمان (عجل الله تعالی ... بازیابی فاضلاب نیروگاه های بخاری ...
زمینه های امنیت جهانی در عصر انتظار نويسنده: فهیمه رئوف چکیدهانتظار، امری پر اهمیت در عصر غیبت امام زمان (عجل الله تعالی ... بازیابی فاضلاب نیروگاه های بخاری ...
بهینه سازی مصرف انرژی در الکتروموتورها (4)
و سرمايه گذاري اوليه در مدت دو سال از محل صرفه جوئي انرژي قابل بازيابي ... پيدا كرده است.18-صرفه جوئی انرژی در تاسیسات آب و فاضلاب شرکت Vacon سازنده درایوهای ... مصرف داخلی نیروگاههای بخاری میتواند بین 5 تا 14 درصد انرژی تولید شده توسط ...
و سرمايه گذاري اوليه در مدت دو سال از محل صرفه جوئي انرژي قابل بازيابي ... پيدا كرده است.18-صرفه جوئی انرژی در تاسیسات آب و فاضلاب شرکت Vacon سازنده درایوهای ... مصرف داخلی نیروگاههای بخاری میتواند بین 5 تا 14 درصد انرژی تولید شده توسط ...
-
گوناگون
پربازدیدترینها